Your B2B partner in
Flanges & Fittings
With over 30 years of experience, INDURA is your reliable expert in flanges, fittings, and other related products. We understand your needs and deliver quality every time.
Find employee
We’re here to provide the support you need, exactly when you need it.
Opening hours
The webshop is always open, but you can reach us here:
Mon-Thurs | 08.00 - 16.15 |
Friday | 08.00 - 14.30 |
As our customer, you’ll get:
Simple and reliable ordering
We make it easy for you to find the right fittings and flanges. With a well-stocked warehouse and efficient processes, we ensure smooth and hassle-free deliveries.
Dedicated customer support
You’ll have a dedicated contact person who understands your business and is ready to assist with product selection, pricing, and logistics. We’re here to help.
Tailored logistics solutions
Whether you need fast delivery, custom packaging, or consolidated shipments, we adjust our logistics to fit your specific needs.
We are experts in
Flanges
Flanges connect pipes, valves, and equipment in industrial systems. They come in various types of steel and ensure tight, durable joints. Flanges are widely used in oil, gas, and other industries for reliable and safe connections of components.
Welding fittings
Welding fittings are used to connect pipes. There are no threads, meaning they can only be connected permanently using welding. Welded caps seal pipe ends hermetically, while welded collars reinforce pipe ends for secure, tight connections in industrial systems.
Threaded fittings
Threaded fittings are components with internal or external threads that connect pipes and fittings in industrial systems. They ensure easy assembly and tight, reliable connections, typically used in plumbing, oil, and gas industries.
We stand by our
Environmental responsibility
INDURA is focused on sustainability by reducing the environmental impact of our products and promoting responsible practices.
Our sustainability strategy has a positive impact on the environment, society, and the economy through responsible business practices.
Save time and minimize costs
We know the manufacturers in the East and Europe and ensure that the goods are delivered on time and at the right price.
Our strict quality control ensures that all suppliers are approved and certified.
We quality check the goods upon arrival at INDURA with visual inspection, measurement control, functional testing, and chemical spectrotesting for flanges made of P and ANSI materials. Our suppliers sign the INDURA Supplier Code of Conduct to ensure high standards.
That’s why our customers choose us
I have a whole project - What now?
Project sales in the flange and fittings industries are crucial for meeting the complex needs of engineering projects.
It involves tailored solutions to specific requirements and coordination with various stakeholders to ensure timely delivery.
The process starts with an analysis of the project’s needs followed by the development of tailored solutions and presentation of offers to the customer.
Once the offer is accepted, the order is implemented with a focus on efficient project management and coordination with production and logistics teams. Communication with the customer is maintained continuously to address any questions or changes.
Our Project Coordinators play a central role in ensuring successful projects and building long-lasting customer relationships through technical expertise and efficient delivery.
We are never far away
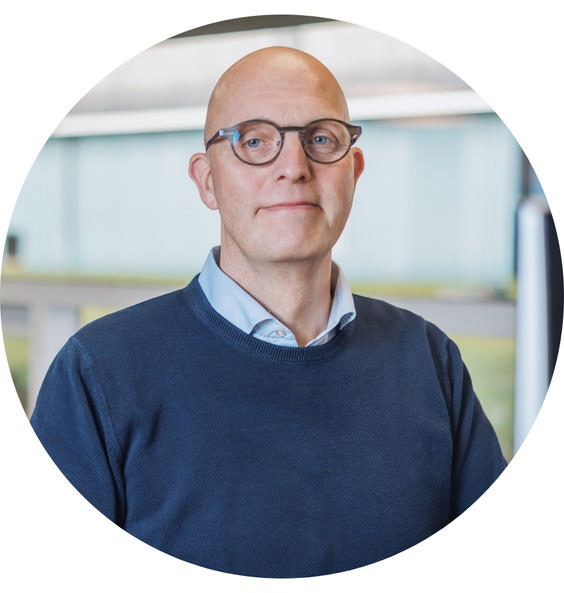
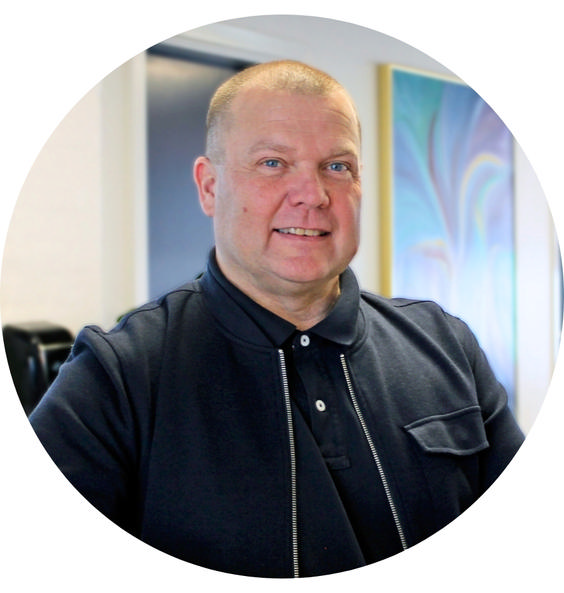
Special Flanges
– exactly as you wish
Our focus on quality and service makes us the ideal supplier of special flanges. We manufacture flanges in size, material, and design according to your specifications.
No minimum requirement
– do you need 2 or 200,000 items?
A wide range of flanges and fittings without a minimum order requirement is essential to meet the varied needs and project demands of different customers. By offering an extensive selection of products in various sizes, materials, and specifications, customers can choose precisely the components that best suit their project without worrying about unnecessary restrictions or imposed minimum order quantities. This flexibility in the assortment allows customers to order exactly the number of flanges and fittings they need without buying more than necessary. It reduces costs and eliminates waste, while ensuring that customers have access to the required components when they need them.